Predictive Maintenance in Construction: Ensuring Efficiency and Safety
In the fast-paced and ever-evolving construction industry, the concept of predictive maintenance has emerged as a game-changer. By leveraging data, technology, and analytics, construction companies can now predict equipment failures before they occur, optimize maintenance schedules, and ultimately enhance efficiency and safety on the job site. Today we will delve into the significance of predictive maintenance in construction, explore real-world scenarios, discuss historical context, analyze current trends, and ponder potential future implications of this transformative approach.
Historical Context: From Reactive to Predictive Maintenance
Historically, maintenance practices in the construction industry were primarily reactive. This means that equipment and machinery were only repaired or replaced after a breakdown or failure, leading to unplanned downtime, costly repairs, and compromised safety. As the industry evolved, a shift towards preventive maintenance took place, where maintenance tasks were scheduled at regular intervals to prevent failures. While this was an improvement over reactive maintenance, it was still not optimal in terms of efficiency and cost-effectiveness.
The Rise of Predictive Maintenance
Predictive maintenance represents the next evolutionary step in maintenance practices. By harnessing the power of data analytics, sensors, Internet of Things (IoT) devices, and machine learning algorithms, construction companies can now monitor the health and performance of their equipment in real-time. This proactive approach enables them to detect anomalies, identify potential issues, and predict when maintenance is required before a breakdown occurs.
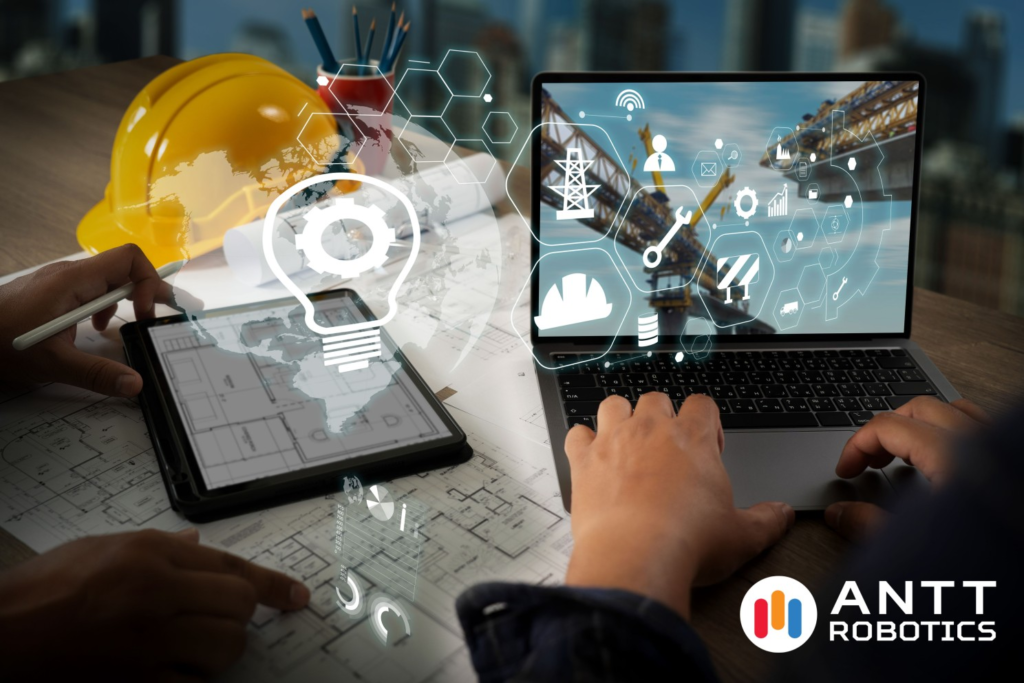
Real-World Scenarios: How Predictive Maintenance Works in Construction
Scenario 1: Monitoring Crane Health
Imagine a construction company that is using a fleet of cranes on a major project. By implementing predictive maintenance, sensors installed on the cranes continuously collect data on parameters such as load capacity, operating temperature, and vibration levels. This data is then analyzed in real-time, allowing the company to identify any deviations from normal operating conditions. If a potential issue is detected, maintenance teams can be notified to inspect the crane and take preventive action before a failure occurs.
Scenario 2: Predicting Conveyor Belt Failures
In another scenario, a construction site relies on conveyor belts to transport materials efficiently. Through predictive maintenance, sensors embedded in the conveyor belts monitor factors like belt tension, speed, and alignment. By analyzing this data using predictive algorithms, the company can anticipate when a belt is likely to fail due to wear and tear. This foresight allows them to schedule maintenance during off-peak hours, minimizing disruptions to workflow.
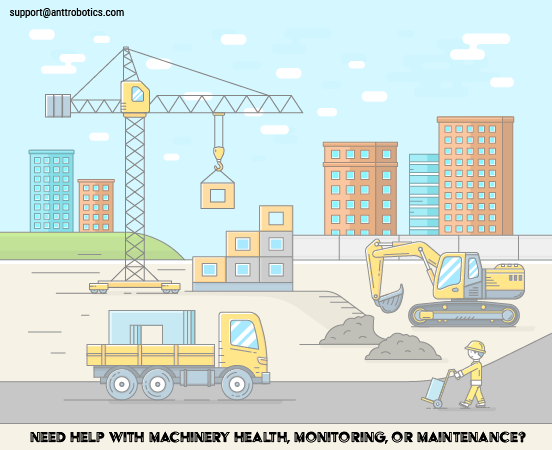
Current Trends in Predictive Maintenance
- Adoption of IoT and Sensor Technology
Construction companies are increasingly embracing IoT devices and sensors to collect real-time data from their equipment and machinery. These devices provide valuable insights into equipment performance, health status, and usage patterns, enabling predictive maintenance strategies to be implemented effectively.
- Integration of Data Analytics and Machine Learning
The integration of data analytics and machine learning algorithms has revolutionized the way predictive maintenance is carried out in construction. By analyzing large volumes of data, identifying patterns, and predicting future maintenance needs, companies can optimize their maintenance schedules, reduce downtime, and extend the lifespan of their assets.
- Shift towards Condition-Based Monitoring
Condition-based monitoring, a key component of predictive maintenance, involves monitoring the actual condition of equipment in real-time to determine when maintenance is needed. This approach allows construction companies to move away from fixed maintenance schedules towards a more dynamic and responsive maintenance strategy.
Future Implications of Predictive Maintenance in Construction
- Improved Safety and Risk Mitigation
By proactively identifying potential equipment failures and addressing them before they escalate, predictive maintenance enhances safety on construction sites. This proactive approach helps mitigate risks associated with equipment malfunctions, ensuring a safer work environment for construction workers.
- Cost Savings and Operational Efficiency
Predictive maintenance can lead to significant cost savings for construction companies by reducing unplanned downtime, optimizing maintenance schedules, and extending the lifespan of equipment. By minimizing costly repairs and maximizing operational efficiency, companies can improve their bottom line and competitive advantage in the industry.
- Enhanced Sustainability and Environmental Impact
By optimizing equipment performance and reducing unnecessary maintenance activities, predictive maintenance contributes to sustainability efforts in the construction industry. By extending the lifespan of assets and minimizing resource waste, companies can reduce their environmental footprint and operate in a more eco-friendly manner.
Learn how predictive maintenance can help you!
Conclusion
In conclusion, predictive maintenance is a transformative approach that holds immense potential for the construction industry. By shifting from reactive and preventive maintenance to a proactive, data-driven approach, construction companies can enhance efficiency, ensure safety, and drive innovation in their operations. As the industry continues to embrace digitalization and advanced technologies, the adoption of predictive maintenance is poised to revolutionize construction practices and set new standards for excellence in the field.
Remember, in construction, prevention is always better than cure. Embrace predictive maintenance and pave the way for a safer, more efficient, and sustainable future in construction!